In the steel drum production workshop, due to the use of multiple spot welders, projection welders and seam welder equipment, power supply fluctuations and problems affecting welding quality often occur in the workshop, and even trips, power failures, and other problems often occur. Sometimes other problems occur. The barrel making equipment also suffers from different degrees of interference, which seriously affects normal production. These problems are generally caused by the use of simple cosine (cosφ) compensation for the power supply in the shop.
I. Causes of Power Supply Interference Problems in Steel Tank Welding Workshop
The problem of power supply and management in the steel drum production workshop where resistance welding is concentrated is not a problem of ordinary electricity and power supply. Drum welding workshops have special rules for their electrical loads.
The thyristor AC voltage regulator welding power supply is used on general steel drum welding equipment. These welding power sources are respectively connected to the three-phase power supply cables in the workshop according to the principle of load balancing. As shown in Fig. 1, the three-phase U, V, and W cables are the secondary (380V) output of the workshop transformer substation power transformer.
Fig. 1 Grid connection of several welding equipments in the drum workshop
Each welding power source includes a welding transformer, and all power loads including transformers are inductive loads. Since the steel drum workpiece also has a certain resistance (resistance welding of the workpiece is formed as shown in Figure 2, mainly the contact resistance of the workpiece and the inductive reactance of the secondary circuit), the resistance of the workpiece is taken into account, and the resistance welding load is taken into account. The nature is sensible.
Figure 2 Composition of resistance welding inductive load
1- Upper electrode; 2-Workpiece; 3-lower electrode; 4- Inductance of secondary circuit
It should be noted that the inductive reactance part of the resistance welding inductive load includes not only the self-inductance of the primary and secondary sides of the welding transformer, but also the mutual inductance between the primary and secondary sides, and the extension of the workpiece to the secondary. Inductance caused by the inside of the side loop.
During the welding process, as the workpiece extends into the interior of the secondary circuit and the influence of the shunt resistance of the welded nugget, the property of dynamic resistance of the resistance welding load is added to the property of resistance.
Due to the complexity of resistance-inductive loads during resistance welding, a high-power thyristor AC switch is used in the main power supply circuit of the welding power supply, resulting in power supply—dynamically changing resistive inductive loads, multiple thyristor phase-controlled adjustments. The following features of the pressure system:
1. The welding current itself is a "off" (not connected) non-sinusoidal waveform (as shown in Figure 3).
2. The load has a varying power factor (angle). When an integral welding transformer is used in a resistance welding machine, the power factor (angle) is roughly in the range of: cosφ=0.9~0.6 and φ=9°~70°. This shows that 10% to 40% of the total current supplied by the power supply to the load during resistance welding is reactive current. The large reactive current means that the power factor of the steel drum welding shop is very low, which requires the power factor compensation of the power grid and the increase of the power supply (power transformer) capacity (kVA number).
From the perspective of power supply, there is a huge waste in the use of the power supply capacity in the steel drum welding shop. From the perspective of the welding process, there is no sufficient welding current and no qualified welding quality (melt nugget). This contradiction between the "capacity waste" and the "need to guarantee quality" power supply and demand is very prominent in the steel drum welding workshop.
Figure 3 Welded thyristor voltage regulator power supply circuit waveform
3, due to the resistance of the resistance welding load, resulting in high-power thyristor AC voltage regulator circuit (that is, the main power supply circuit of the welding power supply), will have a transition process of inrush current, the value up to several times or even more than a dozen pure resistance load Times, plus the steel drum welding workshop is a large, concentrated application of resistive inductive loads, and its overall "effect" is to "distort" the sinusoidal grid voltage into the waveform distortion of the grid as shown in FIG.
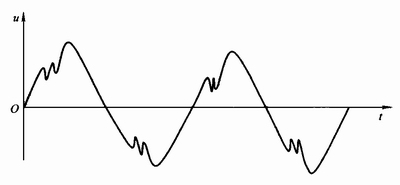
Fig. 4 Distortion of power grid waveform in drum resistance welding shop
This distorted grid voltage waveform can cause strong electromagnetic interference to the power supply of the common power transformer, the welding power source, the control power of the welding power source, and the control devices at various levels.
From the point of view of each welding power source, the electromagnetic interference generated by it during welding is “disturbedâ€; at the same time, it is also subject to “interferenceâ€. The general situation is: often there are unexplained welding program disorders, welding current is not normal, and even welding equipment is sometimes "gone."
Second, to solve the problem of power supply interference in steel drum welding workshop
The main power management measures to solve the above problems are:
1. Install “anti-interference†circuits on each welding power source.
Each resistance welding machine controller should have a random automatic detection of load power factor (cosφ) and current and network pressure fluctuation compensation functions and a more advanced controller.
Resistance welding controller should provide welding current automatic compensation mode, that is, constant current ACC, and grid voltage automatic compensation mode, that is, constant voltage AVC, for the operator to select different modes according to the specific situation of the power grid according to the welding process requirements of the workpiece.
2. On the power supply management computer in the workshop, install the “resistance welder power management software packageâ€. Its main function is to limit the number of resistance welders that have “welding power interruption application†at the same time so as not to use power grid overload.
When the power supply is seriously insufficient, when the welding equipment is not working, the power supply voltage is almost normal (360V~410V); when the welding equipment is working, the current sharply increases, causing the controller power supply voltage to drop to about 200V or even lower, especially if When a Taiwan-powered resistance welding machine is simultaneously connected to a single-phase power supply and used at the same time, there will be a serious shortage of the strength of the welding workpiece (the quality of welding is degraded), and at the same time the instability of the controller operation. When the power supply voltage fluctuates in a wide range, it will inevitably lead to unstable and inaccurate welding energy and welding time of the controller.
When the welding equipment welding parameters are not properly adjusted, such as the welding time adjustment is too long or too short, the welding energy is adjusted too large or too small, it will result in the welding performance of the welding workpiece can not be guaranteed. To this end, foreign advanced workshop power supply management software includes power management software for resistance welding equipment. Its control strategy is to monitor each single-phase power supply line with a highly sensitive voltage monitor. When it is monitored that the voltage of one of the lines is lower than the set value, an interrupt is applied to the main PLC. The interrupt program first checks to what extent the line voltage is low and then processes them separately. The interrupt program will schedule the welder hung on the line according to the scope of the process approval, and pass it on the field industrial bus and the PLC on the control device, so that it can command the welding equipment on the line to be electrified and welded in order so that each Each welding device has enough operating current.