I. Global Tri-Sure Blockers
Our company's Tri-Sure closures are manufactured and used all over the world, laying the foundation for the global drum closure system. The Tri-Sure sealer was created in 1920. It is the earliest sealer system in the world, so it has also become the "industry standard" for steel barrels and plastic barrel sealers in the world.
Our global organization is distributed as follows:
Manufacturing, Sales and Divisions: Netherlands Amsterdam
American Carroll
Rouen, France
Brazilian araucaria
Mumbai, India
Sales and Divisions: Haan, Germany
Italy Milan
Spain Reese
Moscow, Russia
Argentine Rules
(United Kingdom)Dyside, United Kingdom
Mexico, Naukpin
South Africa Durban
Australian Panris
Singapore Singapore
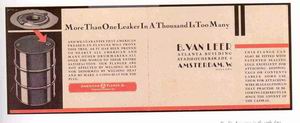
II. The invention of 1920 and today's innovation
Although the current product has been improved in terms of manufacturing and quality, the Tri-Sure closure system still retains the original design of the closure.
By the end of this year, we have been constantly making small changes to our design and innovative designs to ensure that we continue to meet the needs of consumers and meet the industry's services and supply.
Please note our development at each step:
Ribbing, thread rolling, thread high-speed tapping [thin coil low seat and DFT coil, after 1984]
High-Performance Double Gasket Sealing System [4S Gaskets, After 1994]
Tri-Sure nylon screw plug
Anti-intrusion and anti-extrusion screw plug design [R-type screw plug, after 2003]
III. Today's speech content
International Standard [ISO 15750]
Perfect service system
Performance Test International Standard [ISO 16104]
Tri-Sure nylon screw plug
Unscrew and screw in steel screw plug [R type screw plug]
IV. International Standard ISO 15750
In April 2002, the International Organization for Standardization issued the international standard ISO15750 for steel drums.
The first part: open steel drum
Part II: Closed Steel Drums
The third part: embedded type closure system
Type A closures are based on the Tri-Sure closure system.
Type B closures are based on Rieko serrated spiral seat closures.
The C-type closure is based on the Enemoto hexagonal G3/4 closure [JIS].
V. Perfect service system
Tri-Sure coil application on steel drum production line [Type A Knurl].
* Tri-Sure insert lock
* Horn lock for bulk closure
* Single and double locking for closed and open drums
* "Traditional" insert locking for quick-change parts
It is recommended to install a coil insert lock leak detection system to maintain the tightness of the lock washer.
Application of Tri-Sure screw plugs in the end of drum production lines and filling lines.
* Manual Conventional Trisur screw driver
* Manual pneumatic screw plug wrench
* Manual pneumatic torque control screw driver
* Manual Electric Torque Control Screwdriver
* Fixed Electric Torque Control Screwdriver
* Automatic screw plug wrench for production line
Recommended drum filling production line adopts this standard screw plug to tighten wrench [ISO 15750]
The G2 & G3/4 Tab-Seal covers the end of the drum production line and the filling line.
* Manual capping tool
* Manual wind cover tool
* Pneumatic capper on automatic production line
Using our comprehensive global service system can provide our customers with powerful technical support.
Performance Test International Standard ISO 16104
In May 2003, the International Organization for Standardization issued ISO 16104, the performance test method standard.
The performance test items for steel drums include leak test, drop test, stacking test, air pressure test and hydraulic test. These performance tests are to guarantee the critical quality requirements of steel drums in the transport of dangerous goods.
In recent years, the steel drum manufacturing industry has continuously improved its seal structure, seal packing, production process and structural design.
The drum sealer is a complete part attached to the drum. Tri-Sure, as the maker of the closure, will strictly follow the standard requirements to provide the barrel making industry with high quality products and services.
The sealer performance test required in the international standard:
Recently, due to improvements in the G2 screw plugs, the Dutch testing authority conducted the following tests on steel drums:
Drop test, sealer at 8 o'clock position
216 litres closed drum, 1.5/1.2/1.5 mm, drop height 3.0 m
Standard marking: UN 1A1/X1.8/500/03/NL/SL 2490 (mechanical crimping)
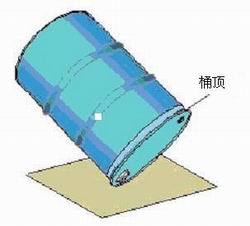
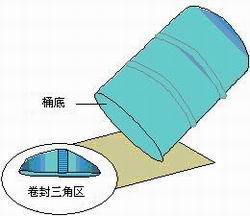
·hydrostatictest
216 l closed drum, 1.5/1.2/1.5 mm, test pressure 700 kPa
Standard Mark: UN 1A1/X1.8/500/03/NL/SL 2492 (weld position)
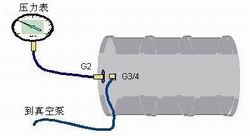
After comprehensive tests, all steel drums were tested by the Dutch authorities and marked with the UN standard.
The sealer's in-plant test items include:
- Torque seal test [washer subjected to a maximum torque of 2.5 Bar]
- Washer wear test [speed, torque]
- Knurled locking performance [measured before and after thread lock]
- Cover leakage test [2.0 bar pressure and vacuum]
Seven. Tri-Sure nylon screw plug
When steel drums are used to package flammable liquids, safety becomes more important.
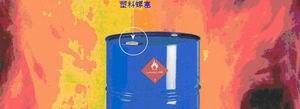
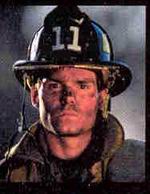

Screw in and out of steel screw plug (R-type G2 screw plug)
More and more steel drum makers and fillers are starting to use automated production lines for screwing in and out. However, it is not easy for the steel drum plugs to be handled in line with the rapid production line. It is generally difficult to accurately screw in and out. To meet the requirements of the rapid production line, it is more difficult for the closure producer. For this reason we have developed a new R-type screw plug that will allow it to achieve optimum results in the production process.
First of all, we have to explain two issues to consumers... squeeze in and squeeze out.
"What is crowding in?"
Drum fillers often see this kind of intrusion. Standard screw plugs In certain situations, when the coil is screwed in, the gasket is pushed into the thread of the coil, sometimes because the gasket is in a state of being twisted on the screw plug.
In this case, the turning thread can damage the gasket. The potential danger is that the damaged gasket can contaminate the barrel or cause the automatic production line to stop production.
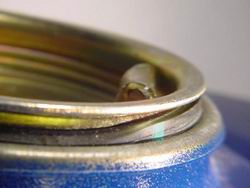
"What is extrusion?"
Drum makers and fillers often encounter this phenomenon. In certain situations, the spiral washer will be forced out of the screw plug and the coil when the screw plug is about to end.
This situation increases the risk of leaking steel drums and difficulty in installing the cover, and may cause the production line to stop working.
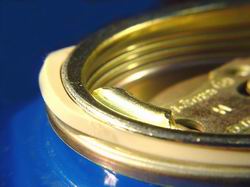
"What improved?"
Now, as long as Tri-Sure steel coils are used, these problems will become a thing of the past.
The screw plug's washer seat has a flange. Our design changes the angle of this flange to make it smaller so that the washer cannot be easily extruded from the screw plug. We recommend using standard torque to tighten the screw plug.
By the same token, we have newly designed a ring-shaped small "flange" between the washer flange and the thread of the plug.
This retaining ring is parallel to the plug flange, which enables the gasket to remain in place when the plug is not tightened, to avoid the risk of the gasket being squeezed into the coil.
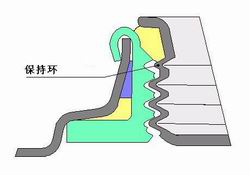