At this time, China has become the world's number one manufacturing country for five years.
In 1990, after 12 years of reform and opening up, China’s manufacturing output accounted for only 3% of the world’s total manufacturing output, while China’s population accounted for 20% of the world’s population. This embarrassing figure reflects the weakness of China’s industrial base. . After a generation of efforts, in 2010, this number became 19.4%, and 18.2% more than the United States became the world's largest manufacturing power.
The rise of Chinese manufacturing has shaken the Western world and has become a catalyst for its revitalization of manufacturing. In his State of the Union address, Obama said that the world's most powerful country (referring to the United States) could not maintain its advantage after a manufacturing crisis, and the United States must catch up.
Britain has no hope of becoming the most powerful country in the world, so observations from the UK are much more calm. "Financial Times" veteran journalist Peter Marsh said in his book "New Industrial Revolution" published in 2012: China won manufacturing, but lost research and development.
He analyzed that China's manufacturing is not as strong as it seems. The key factor in China's manufacturing scale is its population, which accounts for 19.4% of the world's manufacturing industry, but it is roughly equal to the population. More importantly, due to weak research and development capabilities, China's huge manufacturing output can only bring limited real value. For example, an iPhone has an ex-factory price of $179 (output value), but the Chinese factory only takes $6.5 because IPhone parts come from countries such as Japan, South Korea, and Germany, and China is only responsible for assembly. After the iPhone is exported to the United States, it costs $500. The extra $321 is half of the channel's income, and half of it is Apple's profit.
Fortunately, the Chinese government has a clear understanding of this. "China Manufacturing 2025" writes: "China's manufacturing industry is still large but not strong, and its independent innovation capability is weak. The key core technologies and high-end equipment are highly dependent on foreign countries. The manufacturing innovation system of the main body is imperfect; the product quality is not high, and the world famous brand is lacking; the resource and energy utilization efficiency is low, the environmental pollution problem is more prominent; the industrial structure is irrational, the development of high-end equipment manufacturing industry and production service industry lags behind; The level is not high, and the integration with industrialization is not deep enough; the degree of internationalization of the industry is not high, and the ability of enterprises to operate globally is insufficient. The task of transformation and upgrading and leapfrogging development is urgent and arduous."
Obviously, the key to upgrading China's manufacturing is to break through the technical bottleneck. There is no romantic music in technological innovation. It is impossible to rely on XX thinking to become a Buddha. This is a difficult journey that has no shortcuts.
In the catch-up of key technologies, China has had the path of original innovation that is self-reliant, or to follow the example of Japan and South Korea, and to introduce the road of absorption and innovation. The latter quickly gained the upper hand, but after 30 years of practice, various industries The results are very different. Some have fallen into the vicious circle of "introduction → backwardness → re-introduction → then backwardness", such as a considerable part of the equipment manufacturing industry; some hold high the market for technology, but have given up the market but have not exchanged technology, such as cars; Some have finally entered a virtuous circle after twists and turns, such as nuclear power; some are controversial, but they have achieved leapfrog development in the short term, such as high-speed rail.
High-speed rail is the representative work of China's manufacturing industry “introduction → digestion and absorption → re-innovationâ€. The leaping development of high-speed rail has benefited from the previous technology accumulation of the domestic rail transit industry, a strong single introduction subject, the national system of scientific research, and the successful use of the huge domestic market.
In addition, the high-revenue R&D investment of the technology receiving platform, namely the two central enterprises of the North and South vehicles, is also the key. Zheng Gang, an associate professor at the School of Management of Zhejiang University, pointed out in his paper that Japan and South Korea spend 5-10 yuan to absorb and absorb technology for every dollar spent. China is represented by the automobile industry, and for a long time, spend 1 The introduction of the money, only spend 7 cents to digest and absorb. However, in the development of high-speed rail, this ratio reached 1:3, 1 yuan was introduced, and 3 yuan was digested and absorbed. By 2011, CNR Group's R&D investment accounted for 5.1% of its operating income, and CSR Group reached 5.6%.
However, China has not found a second industry to fully replicate the high-speed rail experience, because the railway is China's last government-enterprise industry. In the civilian sector, the Ministry of Railways (now China Railway Corporation) is China's only industry-wide single. Equipment (train) procurement entity.
Therefore, the Chinese telecommunications industry has turned a blind eye to the development of mobile communication standards, which is actually more useful for Chinese manufacturing. It can be said that from 2G to 5G, the journey of Chinese enterprises from the complete no-speaking to the dominant in the standard formulation reflects the ideal path of technological breakthroughs of “government guidance, market-oriented, and enterprise-orientedâ€.
China's independent 3G standard TD-SCDMA is also accompanied by great controversy in the development process, but it turns out that without the 3G's toddler, there is no 4G initiative and 5G's dominant position, and downstream manufacturers cannot form an industry from scratch. scale.
China's telecommunications and railway companies have huge domestic markets to use, but the difference between telecommunications and railways is that China's telecom market has long been a competition for many operators. Although the Ministry of Information Industry has strengthened domestic standards and strengthened its strength. The strongest China Mobile [microblogging] operates domestic standards, but cannot and never intends to use a standard unified market. Domestic standards must face competition from mainstream standards, which forces related companies (operators + equipment vendors) to improve their technology and establish industry alliances. They know that under strong pressure, if they can't afford to fight, the government will give up support sooner or later.
Therefore, in the mobile communication market, the government has played a key role in starting and guiding, but the market law has always played a role, and in the final analysis, the enterprise is the decisive factor.
Since China participated in the 3G standard in 1997, over the past 18 years, many Chinese telecom equipment manufacturers and operators have grown into the top international giants. Among them, Huawei ZTE and other equipment manufacturers account for more than half of the total revenue. In the market, they are faced with complete market competition.
In terms of revenue, Huawei has been the number one global telecommunications equipment company since 2012, and more than 70% of it comes from the international market. In 2014, Huawei also caught up with its own benchmark company Ericsson [microblogging]. This achievement is valuable because it is only in the domestic market and has not been experienced by international competition, even if it is not a real success.
Huawei's success stems from constant technical investment. Since its inception, Huawei has established a system in which R&D investment is no less than 10% of revenue. At present, nearly half of Huawei's more than 170,000 employees worldwide are R&D personnel. In 2014, Huawei's R&D expenditure was 40.8 billion yuan, and research and development accounted for 14.2%.
The proportion of R&D investment in corporate revenue is called the R&D intensity of the company. Research shows that the research and development intensity is less than 1%, the enterprise is difficult to survive; to reach 2%, the enterprise can barely maintain; to reach 5%, the enterprise competitiveness is guaranteed. In major developed countries, the average R&D intensity of enterprises is generally above 2%. Among them, Japan is 3.57% (2009) and the United States is 2.93% (2007).
In 2011, the R&D intensity of China's large and medium-sized industrial enterprises (received more than 20 million yuan) was only 0.93%, and only 19.8% of R&D institutions were established. This data shows that, overall, Chinese companies have not yet established R&D to survive. The consciousness of this.
In fact, Huawei is very rare among Chinese companies. Even Lenovo Group [microblogging], which is the same as Huawei, has a research and development intensity of only 2.6% for one year and less than 1.9% for the rest of the year. In the past 10 years, Lenovo has invested a total of 4.405 billion US dollars in research and development, which is still less than the research and development expenditure of Huawei last year.
This can explain to a large extent why Huawei's roads are getting wider and wider, and Lenovo's days are getting tighter and tighter. Liu Chuanzhi, the founder of Lenovo, said with emotion: "It is a last resort to screw the water out of the towel and it is a struggle. It must have core technology in key areas."
Huawei's success comes not only from technological breakthroughs, but also from breakthroughs in corporate management. Huawei's 2014 rotating CEO Guo Ping once summed up in a speech in June of that year: Huawei's success from the accidental success before 2005 to the inevitable success in recent years is because Huawei has been with IBM [microblogging] since 1999. The consulting company cooperated and cost billions of dollars. The system introduced advanced management software and management methods, and adhered to the guiding ideology of management change that was “first rigid, post-optimized, and re-solidifiedâ€.
This can also explain why many companies, especially central enterprises, have rapid growth in research and development costs, but R&D output cannot grow simultaneously.
Corresponding to the strength of R&D of enterprises is the intensity of national R&D, which refers to the proportion of R&D expenditures of a country to the GDP of a country. China's indicator has made great progress in the past decade. In 2013, it broke through 2% for the first time, and the gap with most developed countries is not big. The current problem is that the capital investment structure is unreasonable, and the second is that the management level leads to inefficient use of funds.
In terms of structure, the company's R&D investment has accounted for more than three-quarters of the total R&D investment in the whole society, but almost all of the R&D investment of the enterprise is used for product development, and only 3% of the basic research is used (2011). However, new technologies, new processes, new processes, and new products must extract “capital†from the basic research reserve. Most of the key common technical problems that are difficult to solve can often find answers in the basic research field. Without basic research, it is difficult to make major breakthroughs in the development level.
This is directly reflected in the status quo of the company's patent ownership. The number of patent applications in China has grown rapidly. According to WIPO data, in 2012, China surpassed the United States and became the largest patent applicant. However, Chinese patents are mainly based on utility model patents and design patents with low technical content. At the end of 2012, China’s invention of valid patents accounted for only 15.7% of all valid patents in China, and the average of the top ten countries in the world was 83.5%.
Market failures should have been corrected by the government, but the government's investment in basic research is just inadequate. The proportion of basic research funds obtained by universities and research institutes in the R&D expenditure of the whole society has been hovering around 5% for a long time, and the developed countries have basically maintained at more than 10%, of which the United States is around 18%, and the European countries such as France and Switzerland are over 25 years. %.
The formation of a country's scientific and technological capabilities is a long-term accumulation process. Europe and the United States have nearly five hundred years of scientific tradition since the Renaissance. Japan has nearly 150 years of scientific tradition since the Meiji Restoration in 1868. These traditions directly correspond to the The number of Nobel Prizes in science reflects the strength of scientific research in various countries.
Since the inception of the first Nobel Prize in 1901 to 2014, there have been 588 people who have won the Nobel Prize in Natural Science (physics, chemistry, physiology or medicine), of which 45.4% are in the United States and 75.5% in the United States, Britain, France and France. 16 people from Japan won the prize and tied for fifth with Sweden.
So far, no one in mainland China has won the Nobel Prize in Science.
In the late 1960s, Japan re-emerged on the ruins of World War II, and caught up with Europe and the United States in the technical level of most important industries, and finally realized its long-cherished wish for centuries. "Made in China 2025" sets the goal of entering the forefront of the world's manufacturing powers and building the world's leading technology system and industrial system by the time of the founding of New China in 2049. Standing in the historical dimension, this seemingly long-term goal is actually a very high demand, a time-critical task.
1) the tensile, compressive and shear strength of Steel Structure is very high, and the section of steel structure is small and the weight is light. High strength of steel structure makes it suitable for the construction of large load bridges; light weight can reduce the base load, and the cost of the foundation, and also facilitate transportation and hoisting.
2) the ductility and toughness of steel is better and concrete, so that the seismic performance of Steel Structure Bridge is better. The seismic and wind resistance are the guarantee of bridge safety. The excellent seismic performance of the steel structure bridge extends its use range, especially in the high intensity seismic area.
3) reduced construction period. The material of steel structure can be rolled into many kinds of profiles, which is simple and rapid. The transportation volume of building materials is less, the construction area occupies a small area.
4) the quality of steel bridge is easy to be guaranteed. Steel structural members are generally manufactured and processed in factories, with high degree of industrialization and high precision.
5) the steel structure is the environmental protection product. The old components removed from the steel bridge can be remelting, saving energy and consistent with the policy of sustainable development.
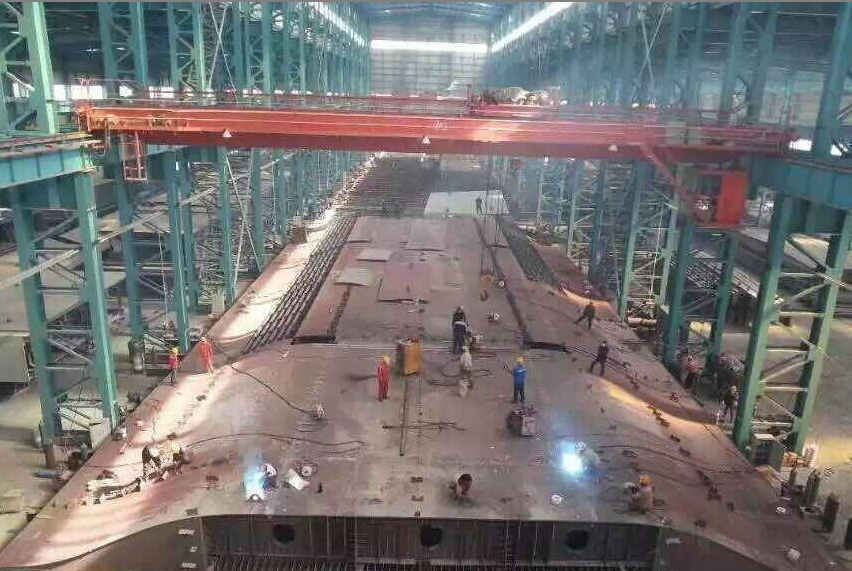
Steel Structure Bridge
Steel Structure Bridge,Steel Frame Bridge,Steel Truss Bridge,Steel Prefabricated Bridge
Zhongda Steel Structure , https://www.zhongdametal.com