The automotive transmission is the core component of the car. As a control device that transmits power, adjusts the rotational speed, and changes the car's forward and reverse, it has a significant impact on the power, economy, comfort, and vibration noise of the entire car. The purpose of the automotive transmission is to match the characteristics of the engine to suit the driving requirements, which requires the transmission gear shaft to function. Gear transmission is currently the most widely used transmission mechanism and can be used to transmit motion and force between any two axes of space. The structure of the gear shaft is more complicated than the ordinary transmission shaft, and the actual damage is complicated by the traditional method, and the calculation result has a large error. In order to provide a theoretical basis for the design of the gear shaft structure, the gear shaft strength of the preliminary structural design can be clearly understood, and effective measures can be taken for the dangerous parts in time. This paper uses the transmission system professional analysis software MASTA to drive the gear shaft of a certain automobile transmission. Analyzed.
This paper takes the gear shaft of a five-speed automotive transmission as the research object. The structural shape of the gear shaft is relatively complicated, and there are special shapes such as key grooves and shoulders, which may cause stress concentration in these parts. It is difficult to accurately understand the laws of stress and strain by conventional checking methods. The transmission system professional analysis software MASTA, with its powerful parameterization function, will be used to establish the parametric model of the gear shaft and import it into the analysis and simulation module of the MASTA software for CAE analysis. At the same time, considering the more complicated parts of the part, revealing the stress and strain distribution law, the static strength and fatigue strength of each gear shaft of the automobile transmission are obtained. According to the analysis results of MASTA software, the rationality of the theoretical analysis and design calculation of the gear shaft of the automobile transmission is verified, which provides a detailed theoretical basis for the structural design and safety of the gear shaft.
Gear shaft function and design requirements
The design of the transmission gear shaft mainly considers the structural form of the gear shaft, the diameter and length of each section on the shaft, the strength and rigidity of the shaft, and the type and size of the spline on the shaft. At the same time, the structure of the gear shaft must also meet the structural layout requirements of the transmission, as well as the processing technology and assembly process requirements.
In order to ensure that the gear shaft works properly under its specified life, the following design principles are usually followed:
1) Select suitable materials, blank forms and heat treatment methods according to the working conditions of the shaft.
2) Reasonable shaft force to increase the strength and stiffness of the shaft.
3) To meet the process requirements, the shaft should be easy to process, heat treatment, assembly and disassembly, inspection and maintenance.
4) The parts on the shaft need to be positioned accurately and firmly.
5) Reduce the stress concentration as much as possible to increase the fatigue strength of the shaft.
6) The diameter and length of each part of the shaft should be reasonable.
Conventional gear shaft calibration method
When calculating the strength and stiffness of the gear shaft by the traditional method, the force of the gear shaft and the reaction force of each bearing are first analyzed, mainly including the force between the gear meshing and the force of other shaft parts. Secondly, since the force and the supporting reaction force of the gear shaft under different gear positions are different, it is necessary to calculate the strength and rigidity of the gear shaft under each gear position. For the calculation of the supporting reaction force on the gear shaft, the calculation should be started from the output shaft, and then the intermediate shaft and the input shaft, and the gear shaft can be regarded as the beam structure supported by the hinge during the calculation process, and the calculated torque of the input shaft. The maximum torque for the engine.
MASTA assembly modeling process
According to the CAD 2D pattern and 3D model provided by the product technical department, a complete MASTA analysis simulation model is established for the vehicle transmission. The model includes cylindrical gears, cylindrical roller bearings, tapered roller bearings, needle bearings, clutches, synchronizers, and housings. In this paper, the automotive transmission is used as a whole for system analysis. On the basis of obtaining the overall stiffness of the system, the static strength and fatigue strength of the gear shaft are obtained.
The material of the gear shaft of the automobile transmission is 20CrMnTi with good mechanical properties. The elastic modulus of the material is 207 000 MPa, the Poisson's ratio is 0.3, the tensile strength is 1100 MPa, the yield strength is 850 MPa, the fatigue strength limit is 525 MPa, and the density of the material. It is 7800kg/m3.
The entire automotive transmission drive system mainly completes the modeling process in the MASTA software design module. The modeling sequence is to establish the model of all gear shafts in turn, determine the spatial position of each gear shaft, and then define other zeros on each gear shaft. Parts such as gear gear pairs, bearings, synchronizers, etc. According to the detailed parameters of components such as gears, gear shafts, bearings and synchronizers, the simulation analysis model of the automotive transmission is established in MASTA software as shown in Fig. 1 and Fig. 2.
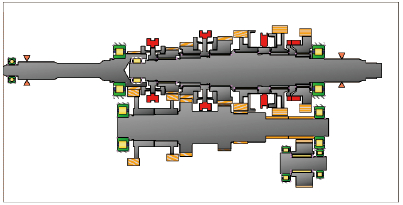
Figure 1 two-dimensional transmission assembly
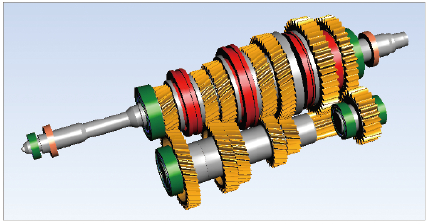
Figure 2 three-dimensional transmission assembly
Gear shaft strength analysis
The traditional method is more complicated and difficult to calculate the calculation of the gear shaft. The MASTA software can accurately and conveniently analyze the deformation, torque, bending moment and stress of the gear shaft under the actual load spectrum. The shaft is subjected to fatigue life analysis to obtain the damage rate of the dangerous section. In the MASTA software simulation analysis process, the allowable fatigue safety factor of the automobile transmission gear shaft is >1, which satisfies the design requirements of the transmission. If it is not satisfied, the cause of the fatigue damage should be analyzed.
The analysis results of the transmission input shaft under the actual load spectrum show that the minimum static strength safety factor and the minimum fatigue strength safety factor appear on the section from the left end of the input shaft at 206.26 mm, respectively 1.451 3 and 1.543, due to the safety factor > 1, indicating that the input shaft can fully meet the strength requirements.
The analysis results of the transmission output shaft under the actual load spectrum show that the minimum static strength safety factor is 1.216 8, which appears on the section 421mm from the left end of the output shaft. The minimum fatigue strength safety factor is 1.570 3, which appears at the left end of the output shaft. At the section of 173.5mm, the safety factor is >1, indicating that the output shaft can also meet the strength requirements.
The analysis of the intermediate shaft of the transmission under the actual load spectrum shows that the minimum static strength safety factor is 3.156 1, which appears on the section 246 mm from the left end of the intermediate shaft. The minimum fatigue strength safety factor is 1.431, which appears at the left end of the intermediate shaft. At the section of 253mm, the safety factor is >1, indicating that the intermediate shaft can also meet the strength requirements, and the static strength safety factor has a certain margin.
Conclusion
The structure of the transmission gear shaft studied in this paper is complicated, especially the stress concentration phenomenon is prone to occur in the transition fillet and bearing fit. It is difficult to accurately obtain the stress and strain law by the traditional check method. With the help of the transmission system design simulation application module of MASTA software, the overall modeling and simulation analysis of the transmission, combined with the actual load conditions of the transmission during the fatigue test, the strength analysis of the gear shaft of the automobile transmission was obtained. The static strength safety factor and fatigue strength safety factor of each gear shaft include the input shaft, the intermediate shaft and the output shaft. The analysis results show that each gear shaft can meet the requirements of use, which indicates that the strength analysis and structural design of the gear shaft of the automobile transmission are more effective by using MASTA software instead of the traditional theoretical calculation method. The analysis result will further optimize the design and safety of the transmission gear shaft. Provide an effective theoretical analysis basis.
Anti Static Flooring,Anti Static Floor Tiles,Anti Static Vinyl Flooring,Anti Static Tiles
JIANGSU HUAJING FLOOR TECHNOLOGY CO.,LTD , https://www.huajing-floor.com